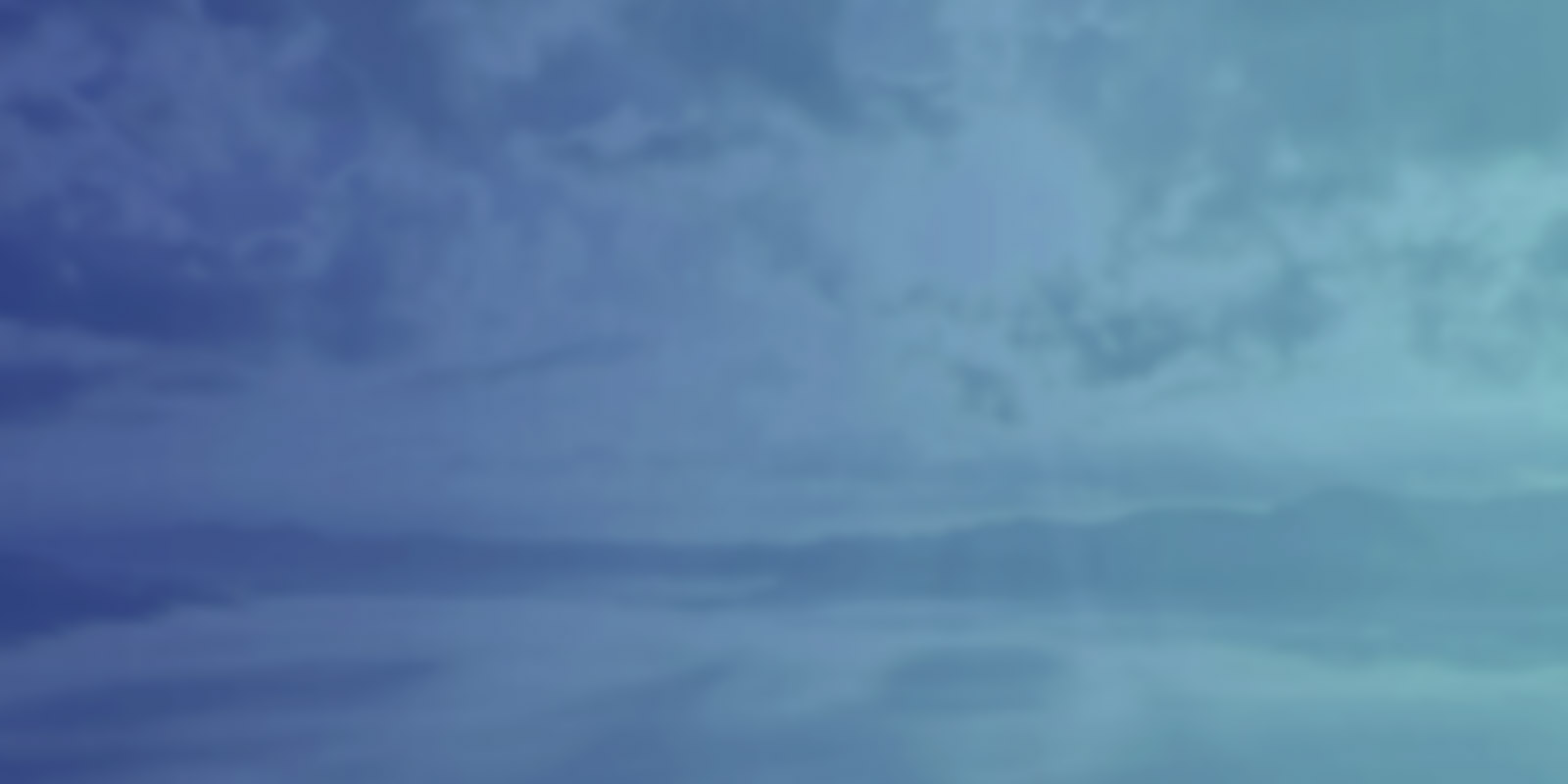
Lower Units | Powerheads | Blocks | Heads | Rods | Crankshafts
MRS maintains the following steps for every gearcase and sterndrive in its line:
Product cores are initially inspected for fatigue and excess wear. Any core disqualified for the remanufacture process is not accepted in the core replenishment process.
Cores that are deemed qualified are brought into the staging area for dismantling, cleaning and a second inspection, both outside and inside the case. Any core that shows any signs of unusual wear, stress or failure are discarded.
Shim surfaces, bearing surfaces and sealing faces are then inspected and measured in order to insure that they meet or exceed original manufacturer tolerances.
Cases for production are bead blasted and are sent through a chemical wash process as well as a hot tank cleaning system to provide for a proper bonding surface for seals and finish coatings. Cases are moved from production to our coating facility, a separate site in the Seminole, Florida area. Here, primer coating is applied to seal the case and provide a superior bonding surface for finish coatings.
A DuPont two-part epoxy paint is applied to each case in manufacturer original colors to minimize corrosion and provide a long-lasting finish indiscernible for the original manufacturer product.
Once completed and cured, cases are returned to the production line where they are re-inspected for color and coating adhesion quality.
Remanufacture of the product proceeds with the identification and preparation of all necessary replacement parts. Only new parts are used for all bearings, gaskets, seals, water pumps, gears and clutches in gearcases and outdrives.
Driveshafts and propshafts are individually cleaned and inspected by technicians. Each piece is accurately measured for straightness as well as all manufacturer provided specifications and tolerances for that particular part. Components not meeting manufacturer specs are discarded and replaced with new components.
At this point the product is moved to remanufacturing clean rooms for the rooms for the final build process where the assembly is performed by certified mechanics.
Upon completion of the build, each unit is pressure tested and performance levels in accordance with manufacturer specifications. Quality control inspections are performed and the unit is packaged for destination routing.
Powerhead cores are thoroughly inspected for signs of corrosion and excessive wear. Any core disqualified is not accepted for the remanufacturing process.
Cores that are qualified for the rebuild process are then sent to the cleaning area. Here they are soaked in a chemical wash to remove all grease and carbon build-up.
After cleaning the core is bead blasted to remove any paint, light corrosion and any remaining exhaust residue. From here the block is sent through a Roto-Jet high pressure cleaning tank. This ensures a completely grit free core which results in a superior quality built product. Each core is inspected and measured against manufacturer specifications. Any core not meeting or exceeding original manufacturer’s specifications is discarded from the process.
Once in our machining area each cylinder is bored to within .002 of finished size.
All cylinders in the block are bored/ honed/ or sleeved to the same size for uniformity. All ports are chamfered to eliminate any ring catching during operation.
After all machining work is completed the block is once again high pressured washed before it is sent to the clean room for final build.
Cylinder heads are sent through the same cleaning process as the block and then checked for trueness or cracks and decked in the machining area as needed.
All rods are chemically cleaned and then checked for any bend or twist.
Crankshafts are magnafluxed and checked for original manufacturer’s specification. After passing the inspection process they are sent for bead blasting and then micro-polished to ensure proper bearing lubrication.
Each powerhead is assembled in a clean and environmentally controlled build room by factory certified technicians. All new pistons with assemblies, wrist pin bearings, rod bearings, crankshaft bearings, gaskets and seals are installed. Every powerhead is painted, serialized and sent to the packing area where it is boxed and put into the inventory system for shipment.